ARP4754A 🡢 ARP4754B
Introduction: Aviation / Systems
ARP4754A is officially titled “Guidelines for Development of Civil Aircraft And Systems”. Rarely can one judge a book by its cover or title; however, in this case, the title literally conveys a powerful message: if you are involved with development of aircraft or systems, you should be well versed in ARP4754A’s ‘guidelines’. Why? There are two key reasons which should be understood before first opening the pages of ARP4754A:
- ARP4754A’s title states “guidelines”, but failure to understand and apply ARP4754A will greatly reduce safety and your ability to achieve certification.
- Where its predecessor ARP4754 was largely similar, too many organizations treated it as “optional” befitting its name “Guideline”; but certification organizations worldwide have formally mandated adherence to this latest version, ARP4754A.
And the 2023 release of ARP4754B updates key areas of aircraft/systems development certification with increased rigor and promotion of modern MBSE systems engineering.
For experienced, proficient developers of aircraft and systems, ARP4754A reads like a book for maintaining good personal health: make a plan for health, understand healthy living, be safe, eat well, reduce stress, exercise, sleep, get regular check-ups, and repeat. For aircraft, an analogous synopsis of ARP4754A would state:
- Plan your aircraft/system’s development lifecycle ecosystem;
- Implement Safety activities per ARP4761/A;
- Define and justify Assurance Level;
- Define System architecture and requirements; Validate.
- Perform Verification and Configuration Management
- Implement Quality Assurance and prove Transition Criteria.
The original ARP4754 standard was first published in 1996 with the purpose of assisting avionics development organizations to think beyond mere hardware and software. Remember, DO-178 (and its European equivalent ED-12) was published over a decade prior to provide guidelines for avionics software. But by the early 90’s it was clear that safe software, and software certification itself, required both knowledge of the system and confirmation of system level safety aspects.
ARP4754 was focused upon aircraft systems whose failure could potentially affect safety of aircraft or occupants. While there are certainly critical stand-alone components on aircraft which could affect safety, ARP4754 is focused not upon components, but rather systems which have complex interactions with other systems on or off the aircraft.
These systems typically involve multiple knowledge domains and are likely to evolve over time. Thus they are developed by different persons via different disciplines often separated by space and time; the best means to ensure safe implementation is via codified development processes based upon deterministic safety: ARP4754.
Table of Contents
ARP4754A VS ARP4754
With revision “A” of ARP4754, e.g. ARP4754A, several key improvements were made as shown below: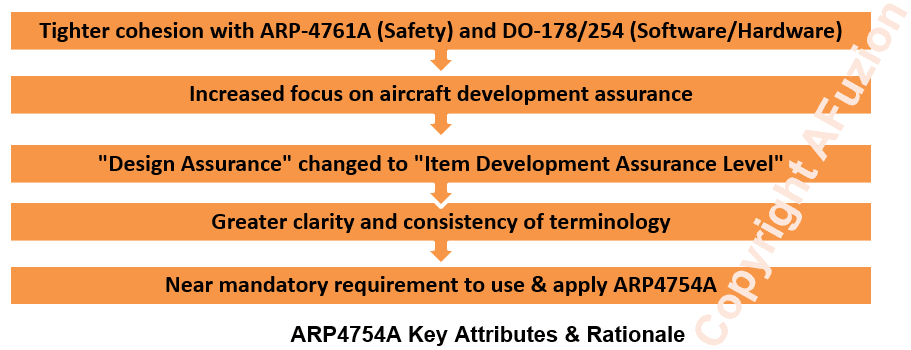
- ARP4754A “Plans” comply with safety requirements and summarize what you will do
- ARP4754A “Processes” state how you will implement the Plans
- ARP4754A “Reviews” (with Checklists advised) denote objective review criteria to determine if Processes were followed
- ARP4754A “Process Assurance Audits” assess conformance of engineering/manufacturing activities, including respective transitions to those Processes and Reviews
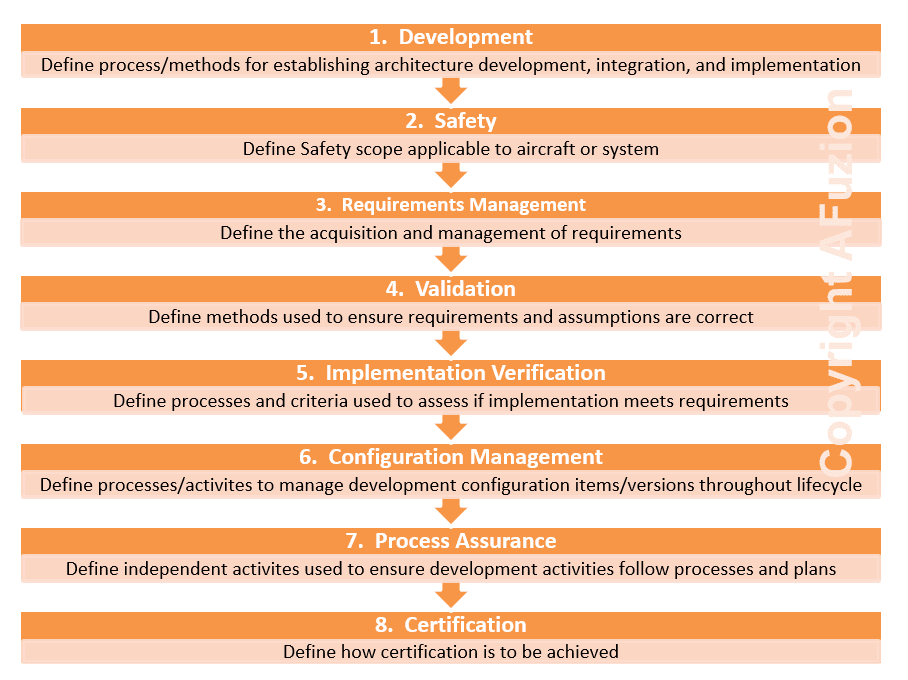
ARP4754B versus ARP4755A
Key updates in the new ARP4754B over ARP4754A include:- Better alignment of ARP4754B to the forthcoming ARP4761A (itself an update over ARP4761)
- Changes to Development Assurance Level (DAL) assignment
- Model-based systems engineering
- Applying ARP4754B’s greatly enhanced “Modifications and Reuse” for aircraft and avionics systems
- Better examples for applying ARP4754B
ARP4754’s Planning Process
- Forcing avionics system developers to consider and specify key engineering processes commensuration with requisite safety implications
- Informing certification authorities to the planned system’s technical and safety attributes, along with corresponding planned engineering activities
- Serve as a means to verify planned versus actual avionics engineering activities
Quick Note on Validation, Verification, Process Assurance, Reviews & Audits
ARP4754A/B Verification is performed by engineering and assesses if implementation meets requirements. Validation assesses the acceptability of those requirements. In the avionics world (and reading between the lines of ARP4754A/B and the DO-XXX documents) it should be understood that at its simplest, “Verification = Reviews + Tests + Analysis.” Virtually everything is reviewed. Requirements and implementation are tested. Analysis is applied when reviews/tests are not 100% conclusive. Audits are process-oriented and performed by independent Quality Assurance (QA), also called Process Assurance (PA), personnel. They are not reviews; instead audits determine if Engineers followed defined processes. For Systems, quality assurance is termed Process Assurance (PA) which is a superset of quality assurance, but the terms are used in aviation almost interchangeably.ARP4754A’s Eight Planning Topics
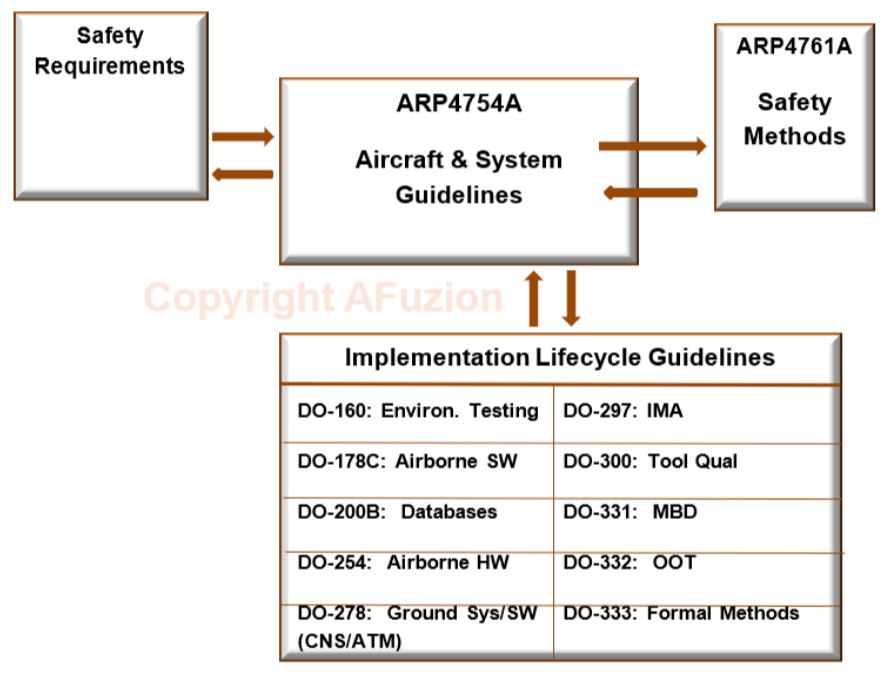
Why ARP4754A? Background
Before delving into ARP4754A specifics, one should truly consider why it exists. When avionics systems were simpler decades ago, it was possible for smart designers to avoid a framework posed by ARP4754A and simply mentally conceive those systems and proceed immediately with implementation. Admittedly today, the need for ARP4754A is less justifiable for simple systems, but such simple systems are becoming fewer and fewer. But for modern aircraft, the number, variety, and complexity of systems continues to grow exponentially. Clearly, avionics systems can be much more complex than commercial brick and mortar buildings, but it would be inconceivable to begin building a commercial office building without a soil/earthquake analysis, foundation design, and a plan for inspections. Those inspections obviously continue throughout the building process including satisfactory electrical, plumbing, emergency exits, and proper reinforcement. While it is possible great builders could possibly build a safe building without detailed plans, blueprints, processes, and inspections, there would be no way to fully verify the building’s “greatness.” Why? “Greatness” must be associated with proof a building is great. Proof is based upon assessing implementation versus plans then correcting any deficiencies found. ARP4754A is aviation’s framework for proving reliable, safe, and reusable aircraft and systems. Clearly, without plans and processes for a building, there is no way to assess, or claim, a building’s design and construction are safe. Since developing avionics can be more complex than constructing a building,it is clear that avionics systems require big-picture planning, processes, requirements, safe development, verification/validation, and evidentiary proof of conformance. Welcome to ARP4754A, “Guidelines for Development of Civil Aircraft And Systems.” With revision “A”, e.g. ARP4754A, several key improvements were made as shown below: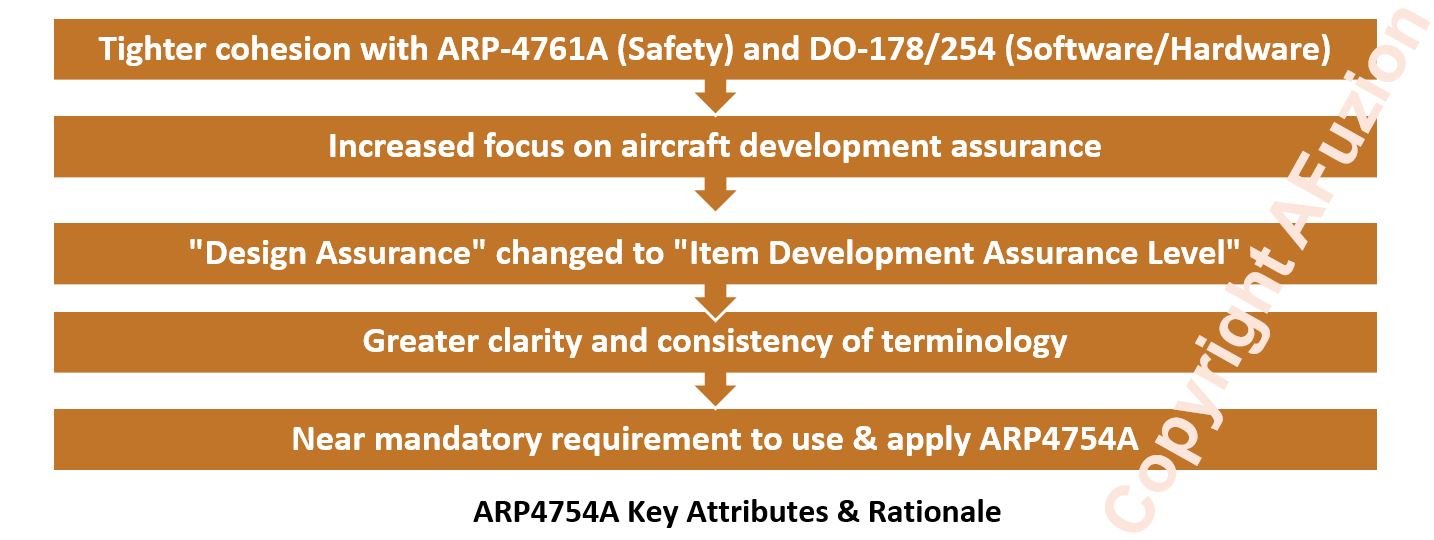
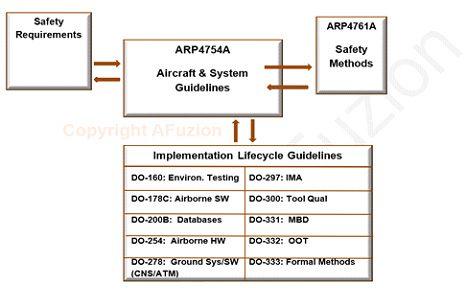
More on ARP4754A VS ARP4754
With revision “A”, e.g. ARP4754A, several key improvements were made as shown below: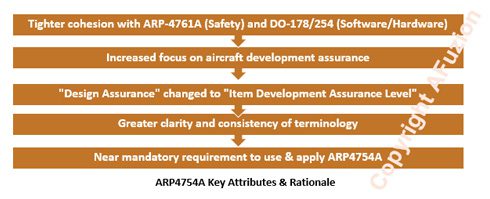
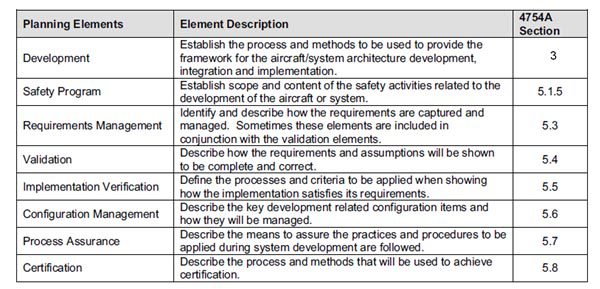
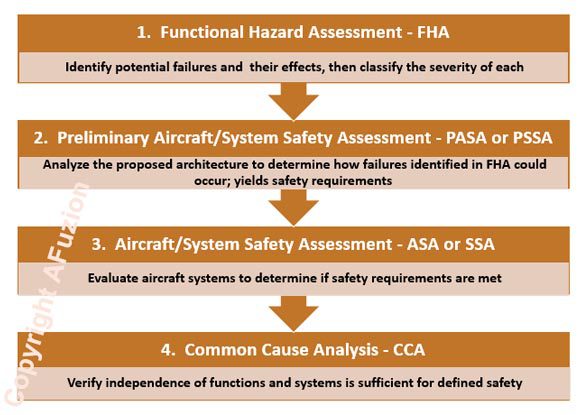
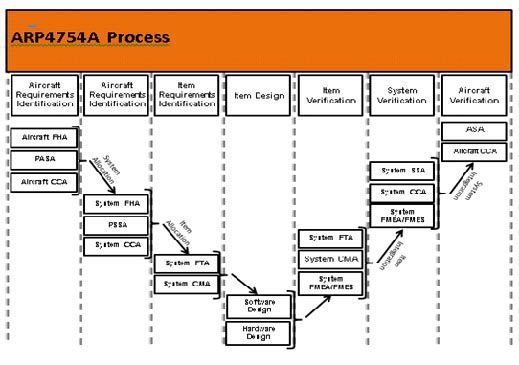
System Safety Assessment (SSA) for ARP4754A & ARP4761A
The ARP4754A / ARP4761A SSA verifies that the implemented aircraft and system designs meet the requirements of the aircraft/system FHA and the Preliminary Aircraft Safety Assessment (PASA) and Preliminary System Safety Assessment (PSSA). The SSA documentation generated during the SSA includes:- Updated aircraft FTAs, system FHAs, and system FTAs per ARP4754A / ARP4761A
- Documentation showing item installation requirements
- Any material used to validate the failure condition classifications
- If necessary, revised maintenance manuals detailing new maintenance tasks aimed at reducing component exposure times
- If necessary, revised flight crew operating manuals detailing procedures to be followed in the event of certain failure conditions
- Functional DAL, called FDAL; and
- Item DAL, called IDAL.
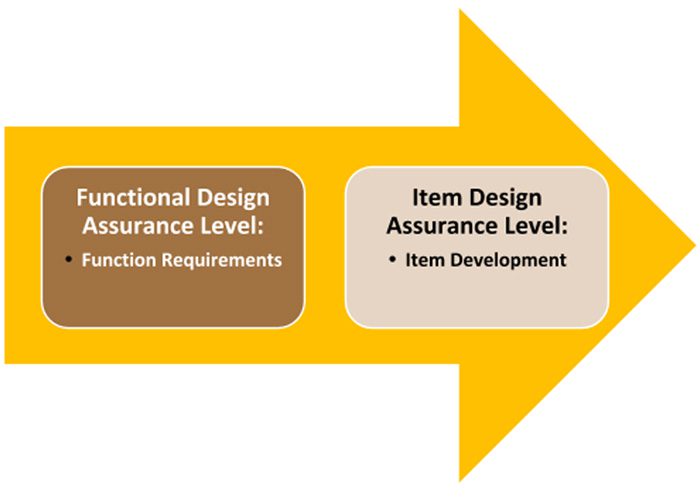
Top-Level Failure Condition Severity Classification: | Corresponding FDAL Assignment |
Catastrophic | A |
Hazardous/Severe-Major | B |
Major | C |
Minor | D |
No Safety Effect | E |
Common Cause Analysis (CCA)
The acceptance of adequate probability of failure conditions is often derived from the assessment of multiple systems based on the assumption that failures are independent. This independence might not exist in the practical sense, and specific studies are necessary to ensure that independence can either be assured or deemed acceptable. The CCA is concerned with events that could lead to a hazardous or catastrophic failure condition. The same software installed on multiple LRU’s is considered by many to be the most often overlooked area of common cause. For example, Dual Flight Management Systems (FMS) could fail under the exact same conditions if the same software is installed on both units.Defining Requirements
You have the DALs are defined and it is time to define requirements. What? Requirements are not considered during the DAL assignment process? While it’s common to know, or at least initiate, the requirements in parallel with the DAL assignment process, the DAL is about safety and thus should be initiated without formally considering the requirements. Safety considerations need to precede functionality. Requirements are defined partly to satisfy safety, as determined via the DAL process. So DAL determination precedes requirement definition. How are requirements defined? By considering the various types of requirements and how each pertains to the aircraft or system being developed. The following figure depicts the primary types of requirements which must be defined, along with the common (but not mandated) order: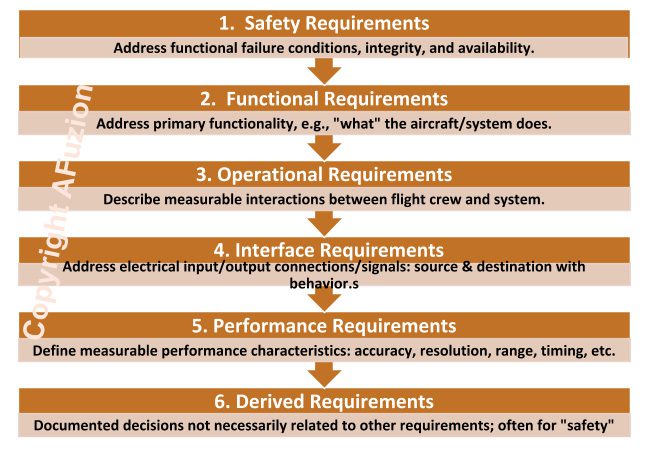
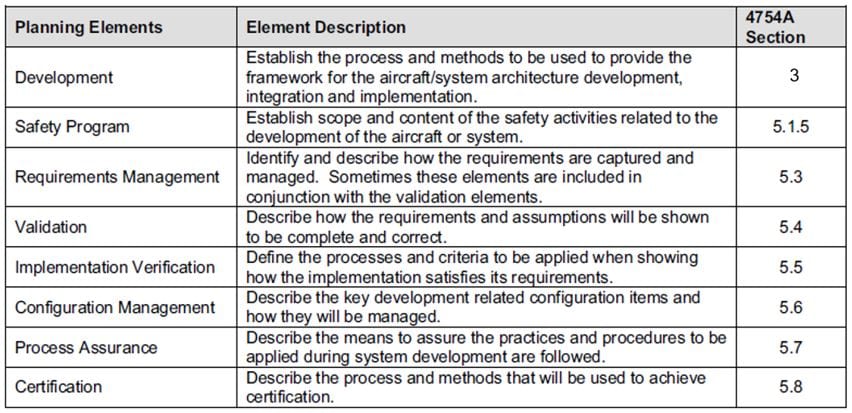
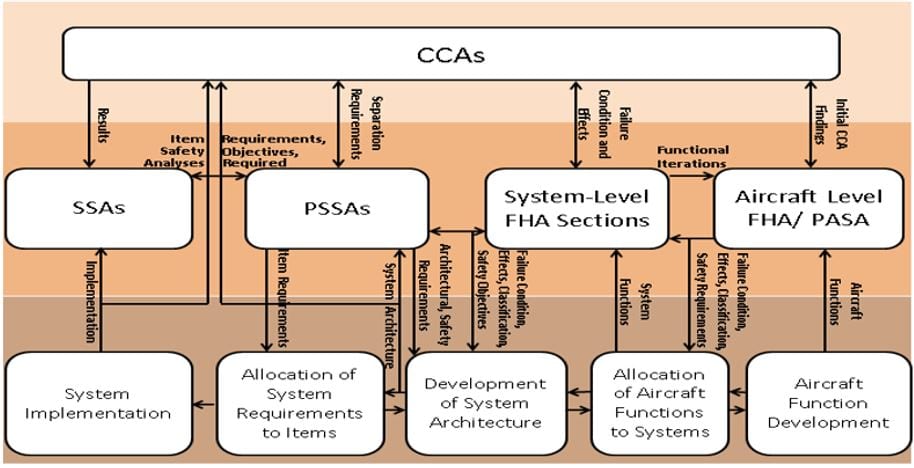
Functional Hazard Assessment
The objective of the FHA is to identify functions, failure conditions of functions (loss of function, malfunction, etc.), and their classification (catastrophic, hazardous, etc.) so that aircraft and system designs may be proposed and achieved which decrease the probability of the occurrence of the failure conditions to acceptably lesser levels. It should be noted that in some cases, total loss of a function is not as impactful as partial or misleading loss of functionality; a pilot may be more likely to mitigate total loss of one system’s functionality by switching to a different system.Preliminary System Safety Assessment (PSSA)
The PSSA is a set of analyses normally performed during the system requirements and item requirements phases of the aircraft life cycle. The PSSA is where the proposed aircraft and system architectures are evaluated and defined; this provides the ability to derive system and item safety requirements. The input documents to the PSSA are the aircraft FHA, preliminary aircraft Fault Tree Analysis FTA (and allocation of failure budget against the top level failure requirement), and the system FHAs. The documents produced during the PSSA are the updated aircraft and system FHAs, updated aircraft and systems FTAs, and the preliminary system Common Cause Analyses (CCAs).The PSSA is a continuous and iterative process. The objective of the PSSA is to determine how the aircraft and system failures can lead to the hazards identified in the FHAs and to determine how the FHA requirements can be met. The PSSA is often associated with the Preliminary Aircraft Safety Assessment (PASA). An important note: Appendix 1 of AC23.1309-E has some useful guidance to assist with assessing the severity of failure conditions of aircraft functions and systems at this stage of the project.Requirement Validation
Congratulations – the aircraft and system requirements are captured and it’s time to initiate design then implementation. But you’re smart and you know you will verify those requirements later to ensure implementation satisfies the requirements. Wait: how do you know you have the “right” requirements? Exactly. That is the role of requirements validation and it must precede design/implementation. Why? Requirements are the foundation to aircraft and systems. Like building a house, changing the foundation after starting construction is undesirable for many reasons, most important of which is safety. Truly, you need to determine if you have conflicting, incomplete, or incorrect requirements long before you initiate development. ARP4754A requires a formal validation process whereby requirements are evaluated for correctness and completeness before they are used in design/implementation. However, requirements validation is performed throughout the development process because changes are inevitable and all changes to requirements or anything affecting a requirement must be assessed through validation. The approach to requirements validation must be defined in advance via plans; typically a separate validation plan is utilized, however it is common to combine validation planning documentation within the verification plan since validation and verification are related. For ARP4754A and ARP4754B success, most practitioners find ARP4754A training to be helpful. A brief free ARP4754A training video, one hour, is here: https://www.youtube.com/watch?v=tng3rGW-BcQ For more detailed Public ARP4754A training, Private ARP4754A training, and Remote Online ARP4754A training, see the training schedule here: https://afuzion.com/public-training-webinars-2/. Requirements validation is a formal process, and within aviation, most formal processes require checklists. Even a 5,000 hour pilot with vast experience is formally required to follow a checklist for many key activities including takeoff and landing. And because safety is so important, commercial aircraft utilize a co-pilot for added independent verification. Fortunately, ARP4754A provides high-level requirement validation criteria in section 5.4.3 which should be used to form the basis of the validation checklist. For brevity, these are not repeated herein as there is little unique about requirements validation in aviation versus other safety-critical industries (however the term “validation” itself is used differently – see the corresponding Aviation Requirements chapter in this book). The usual evaluation criteria apply: correctness, non-ambiguity, avoidance of conflicting logic, identifiability, traceability, impact upon safety, etc.Implementation Verification
The plans have been followed perfectly, requirements seem to be perfectly validated, and QA has audited the activities throughout the engineering process including all transitions through implementation. Ready to begin flight test? Not so fast. Remember, in aviation, the probability of software error is assumed to be “1”, e.g. errors happen – can they be detected and mitigated? During engineering, the same philosophy applies. While great plans, processes, and engineering produce measurably better systems with fewer errors, verification is still required. The common belief is that verification improves quality by finding errors. While not incorrect, verification is really performed to assess the adequacy of prior activities in conjunction with a feedback loop to improve those activities and the implementation. Therefore aviation verification is more important, and more encompassing, than mere bug detection. It is commonly believed that verification is performed purely to identify errors so that they can be fixed. While partially true, verification at the aircraft and avionics systems level per ARP4754A is more encompassing, as it is also used to assess the completeness and quality of preceding development activities including Safety, Requirements, and Design; not just Implementation. Remember the overly simplistic verification equation cited earlier, “Verification = Reviews + Tests + Analysis” Both the required, and the potential, verification activities are more diverse; keep in mind the degree of verification rigor increases with the DAL rigor, e.g. DAL A is the most intensive. The following figure depicts the common types of verification applied under ARP4754A: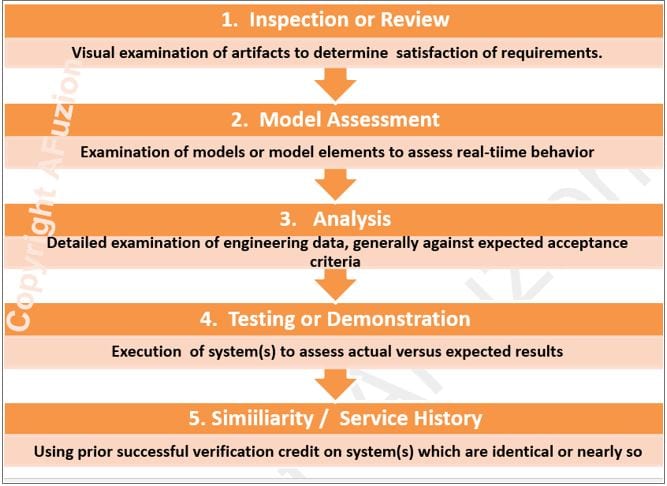
ARP4754A Planning Background
Once acquired and customized on the first project, your ARP4754A team will retain the expertise to create, customize and re-use as appropriate on future ARP4754A projects. Note that the ARP4754A Planning documents can be purchased in either Template form or “Initial Draft” form. The Template form option provides the basic templates which you then modify to create an initial draft. The Initial Draft option provides for AFuzion to first create initial drafts of all planning documents using the same template, but adding the customer’s basic product information to create an initial draft; the customer then must finalize this initial draft to create the first versions of these five planning documents. AFuzion’s ARP4754A Plans and Checklist Templates cover all phases of the aircraft/system project lifecycle, and are developed with ARP4754A in mind. The users of these templates would need to have some basic understanding of ARP4754A, such as attendance at AFuzion ARP4754A training available here: https://afuzion.com/public-training-webinars-2/ These ARP4754A templates and checklists also help in getting organizations to the goal of higher SEI CMM/CMMI ratings (preferably Level 3 – 4+). Usage of AFuzion process templates and checklists are intended to maximize the probability of project success and quality. The regulatory agencies require that most airborne commercial systems operating within commercial airspace to comply with ARP4754A (details can be found in the regulatory website). The planning and processes for the systems lifecycle are required for any ARP4754A project and those processes must be defined before initiating that phase and followed during that phase. Although Checklists are not formally mandated by ARP4754A, your regulatory agencies will require that you prove conformance to ARP4754A according to your approved processes; this conformance is very difficult to achieve and prove without checklists. In fact, nearly all ARP4754A projects use checklists for reviews and proof of such. AFuzion Planning Templates are meant to provide the proper framework for customization to meet the system planning requirements of ARP4754A. Although there is no perfect process for all programs, there are unique areas of each individual project. Each project will vary somewhat in how it chooses to define, implement, or augment the AFuzion Planning Templates. Factors to consider include project Design Assurance Levels, complexity, and expertise of staff, development methodology, tools/environment, and technology. The AFuzion Planning Templates provide the basic elements of an aircraft or avionics project compliant with ARP4754A. Further, AFuzion can customize and tailor these processes by the appropriate amount as an outflow of an AFuzion gap analysis process, upon request as part of the optional first draft delivery. If there are items in the checklists that are not applicable to your program they could simply be answered with “N/A”. It is also recommended that the checklists be placed under your project’s configuration management (CM) system to ensure checklist integrity. Independent reviews are always preferable to reviews done by the developer. It should be noted that the checklists should be widely distributed to all personnel developing any avionics lifecycle item, prior to that person beginning such initiation. Thus, the checklist serves as a “report card” whereby the originator’s success is measured. When the originator understands what the independent verification reviewer will be evaluating the related hardware artifact for, the originator will more productively attain checklist compliance during development of that artifact. This applies to requirements, design, implementation, test, etc. The level of “independence for verification” required by ARP4754A varies according to Design Assurance level (Level A through E).ARP4754A Plan & Checklist Templates Provided by AFuzion
AFuzion ARP4754A Plan/Standard Templates
(email info@afuzion.com for a free sample copy)- ARP4754A PASA Preliminary Aircraft Safety Assessment Template
- ARP4754A PSSA Preliminary System Safety Assessment Template
- ARP4754A Project Specific Certification Plan Template
- ARP4754A Safety Program Plan Template
- ARP4754A System Process Assurance Plan Template
- ARP4754A System Development Plan Template
- ARP4754A System Requirements Management Plan Template
- ARP4754A System Configuration Management Plan Template
- ARP4754A System Validation & Verification Plan Template
- ARP4754A System Requirements Standard Template
- ARP4754A System Design Standards Template
- ARP4754A System Validation & Verification Standards Template
AFuzion ARP4754A Checklist Templates
- ARP4754A Project Specific Certification Plan Checklist
- ARP4754A System Process Assurance Plan Checklist
- ARP4754A System Development Plan Checklist
- ARP4754A System Configuration Management Plan Checklist
- ARP4754A Validation & Verification Plan Checklist
- ARP4754A System Requirements Standards Checklist
- ARP4754A System Design Standards Checklist
- ARP4754A FMEA/FMES Review Checklist
- ARP4754A System Requirements Data Review Checklist
- ARP4754A System Design Review Checklist
- ARP4754A System Validation & Verification Standards Checklist
- ARP4754A System Configuration Index Checklist
- ARP4754A Objectives Checklist
ARP4754B
ARP4754A has evolved to ARP4754B (ED-79A in Europe which is now released and increasingly mandatory; the ARP4754A to ARP4754B transition is depicted in the following Figure extracted from AFuzion’s ARP4754A which is provided via SAE, the group that created and publishes ARP4754A and which has chosen AFuzion to deliver its training (contact SAE to procure ARP4754A training or visit the training schedule here: https://afuzion.com/public-training-webinars-2/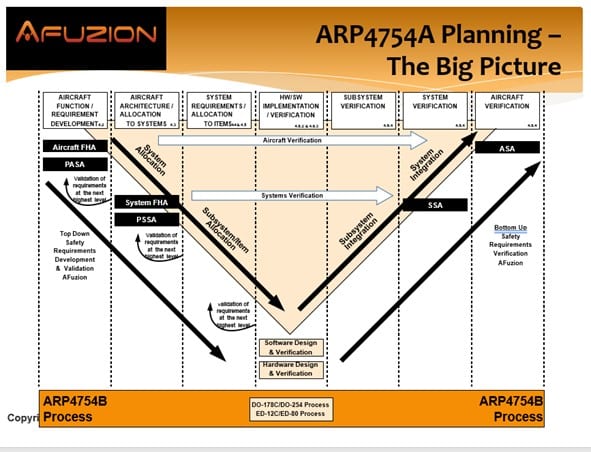
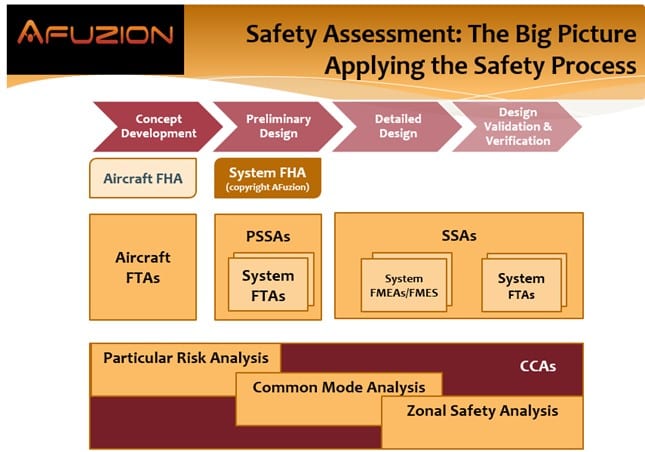
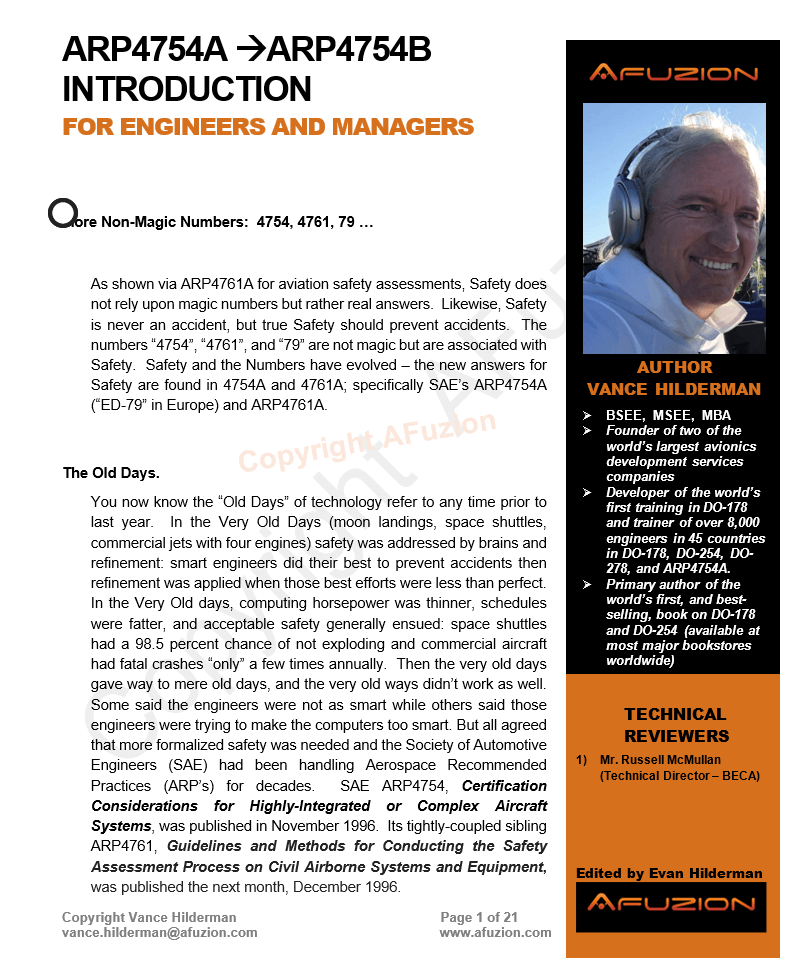
Information Request Form
Please provide the following information to receive your full Whitepaper
For additional ARP4754B and ARP4761A information, see www.arp4754A.org.
Other Free Resources
- Free 30-minute tech telecon to answer any of your tech Q’s
- Free Sample Certification Checklist
- Free AFuzion Training Video Sample
- Request invitations to future AFuzion tech webinars, fee waived (free)